Understanding Maintenance, Repair, and Overhaul (MRO): The following article covered in this guide shall include but not be limited to the following.
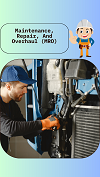
In the current world of industry, productivity and durability of equipment are critical success factors. Machinery and systems maintenance is very important in industries to make sure that they are running as expected and without any unnecessary hazards. This article provides a comprehensive overview of what MRO is, why it is relevant, and how it affects industries.
Introduction to MRO
What is MRO?
MRO is a strategic concept that deals with the management of equipment and machinery with the ultimate goal of promoting reliability and efficiency. They are meant to reduce equipment outages, increase equipment’s useful life as well as adhere to safety specifications. Although MRO is fairly standard in modern maintenance strategies, it is crucial to understand that it can differ from one industry to another, from the type of equipment, and requirements of the operation in which it will be used. As an example, MRO in aviation requires frequent inspections and maintenance routines in order to guarantee safe operation of the airplane; in manufacturing, MRO deals with maintenance of equipment to elimination of stops in production line.
Significance of MRO
MRO activities constitute one of the key processes that should be implemented to ensure a high level of operational effectiveness as well as safety. In any industry, effective MRO can lead to:In any industry, effective MRO can lead to:
- Safety: This means that the equipment is well maintained and any defect that can cause a failure leading to accidents or injuries is taken care off. For example, periodic checks of the airplane engine or safety features of large machinery are performed to correct possible risks at a non-crisis phase.
- Reliability: Operational equipment that are well maintained are less likely to develop some mechanical problems hence there will not be many interruptions with the operations. This reliability is important in industries such as the medical sector because the failure of equipment maybe be costly to patients.
- Efficiency: Optimisation of MRO involves minimising the time that a plant and its machinery spends out of action and guaranteeing that the wear and tear of machinery is properly maintained and its work rate is optimal in order to maximise productivity and decrease costs.
Components of MRO
1. Maintenance
In this case, maintenance refers to all those activities that are directed towards ensuring that the equipment used in the organization’s operations is in proper working condition. It is divided into:
- Preventive Maintenance: This is a process which entails implementation of planned activities whose intention is to minimize equipment fails without having them occur. For instance, replacing the oil in equipment, or cleaning filters in air conditioning and heating systems are preventive measures that users undertake to prevent system failure. Preventive maintenance has elements that center on time-based or usage-based maintenance to ensure equipment before a fault occurs.
- Predictive Maintenance: This approach takes real time data and deploys analytical tools to forecast when the equipment would need maintenance. Predictive maintenance checks the condition of equipments and infers problems that may cause failure; vibration, temperature, and pressure are some of them. Condition and diagnostic monitoring form other screening strategies utilized to predict maintenance requirements and schedule the services appropriately.
2. Repair
Repair entails having to solve problems with the equipment in order to correct and prevent a failure. This includes:
- Corrective Maintenance: Corrective maintenance is done after equipment breakdown because it aims at repairing the equipment after breakdown. The goal is to bring an item of equipment back to its functional state. For example, if a conveyor belt of a factory has developed some problem, the corrective maintenance would include the fixing of the belt or replacement of a damaged part. It is a reactive type of maintenance where tasks are only carried out after breakdowns or after they have occurred.
3. Overhaul
However, the term overhaul signifies a comprehensive inspection and subsequent renovation of equipment. It is usually carried out when equipment is in the last useful life or when there is evidence of major problems. Overhaul includes:
- Disassembly: The equipment is then dismantled down to detail in order to be checked. This process enables technicians ascertain cases of wear and tear or any form of damage, which normally could not be pointed out easily by just looking into the car during road tests.
- Refurbishment: Consequently, components that are outworn or damaged are in most occasion rebuilt or replaced. This may comprise activities like refinishing of part, replacing of bearings, or changing of obsolescent components.
- Reassembly and Testing: The equipment is then reassembled and properly checked for functionality and usability after going through this process of refurbishment. This step helps in affirming that all repair processes were successful and that the equipment can be used.
Importance of MRO
Safety
MRO involves a variety of issues and safety is a paramount factor in any strategy formulated in such a sector. Maintenance and repair of equipment check ensure that they do not fail at the wrong time or even cause accidents or harm to the people around them. For instance, in the aviation industry, the transportation of people and cargo requires a lot adherence to regulation and; hence, scheduled maintenance and inspection of air-crafts are paramount. In this way, MRO practices are aimed at preventing the development of potential problems that can cause failures and contribute to ensuring a safe working environment.
Cost Efficiency
By reducing failure of equipment before their useful periods are over, MRO practices are cost efficient in the organization. This way, through such measures of preventive and predictable maintainability, the occurrence of repairs is minimized, which in turn decreases the expenses on maintenance. Also, through effective MRO, one believes in the ensuing of the costly downtimes which leads to a reduction in productivity and evasion of revenues.
Regulatory Compliance
There are lots of fields where companies are required to adhere to respective rules and regulation and codes which call for periodical checkups and examinations. It is important to follow these rules in order not to be fined and have legal complications. For instance, in the case of medical equipment used in health facilities, machines or instruments must be taken for routine servicing and adjustment to guarantee they conform with the legal requirements and are in proper working conditions as required. Compliance with the MRO is the best way of ensuring that an organization addresses these compliance principles and stays operationally legal.
MRO Business Processes and Practices
Standard MRO Procedures
- Planning and Scheduling: A regular maintenance plan that is likely to be determined by the manufacturer’s standard time, usage of equipment, and previous instances must be observed. Potential maintenance activities and their requirements need to be evaluated; therefore, proper planning of these activities is to decide which of them require further frequency of execution and which resources to allocate to their implementation. Scheduling is also useful in avoiding the breakdown of equipment as well as in the proper planning of maintenance.
- Inventory Management: Pre-stocking of key spare parts and tools should also be made in order to avoid frequent breakdowns that are disruptive to normal operations. For instance when spare parts are critical to operation of the facility that has breakdowns they have to be available in reasonable quantity to avoid forcing the operation to come to a standstill.
- Documentation: Maintenance scheduling, repair or overhaul records of the equipments are useful in assessing the equipment performance rates and history. In the case of documenting, it can be used in detecting patterns of problems, assessing the maintenance of measures, and meeting requirements of code.
Best Practices for Effective MRO
- Adopt a Proactive Approach: By focusing on the predictive maintenance strategies, the potential problems are solved before resulting in a failure. This is because using data and analytics for Maintenance Scheduling in organizations helps to schedule maintenance in advance and prevent breakdown that would be very expensive for the organization.
- Leverage Data and Analytics: The use of data principles helps organizations: Heed to make appropriate decisions on maintenances and repairs. Maintenance analysis of equipment data includes determination of trends, failures chances, and the best time to perform maintenance.
- Regular Training: Cross training is very important in MRO maintenance staff so that they can be update with with modern technology and best practices. Continuity in training ensures that professionals working as technicians are up-to-date on new developments in the industry so that they can enhance their talents and proficiency in the same.
Challenges in MRO
Common Issues
- Unexpected Failures: Machines are liable to breakdown at any one time and thus may result in costly repairs and also hampering of operations. Some failures can be unpredictable and may weirdly be on a critical component that needs attention before it brings the system down.
- Parts Shortages: When it is hard to obtain particular parts, repair work and operations plans can be affected. Problematical here is that parts can either be unavailable in the market, or they have been stocked out by the manufacturers which are key motives that make having back-up plans crucial.
- Aging Equipment: While purchasing used equipment, everyone should remember this fact that older equipment will be needing more repairs and its efficiency will be comparatively less. Old equipment may have issues with regard to maintenance and. duration may be long hence it may be necessary to upgrade or Change them.
Strategies to Overcome Challenges
- Implement Predictive Maintenance: Using of some strategies and methods of maintenance can also allows to avoid failure, as the name suggests, the maintenance is made before failure occurs. Thus, the conditions of equipment shall be observed, and data analysis will allow for prevention of possible failures and taking relevant actions.
- Maintain a Spare Parts Inventory: A maintenance team should ensure that, various parts that may be used frequently during servicing are availed to avoid any form of a break down in the servicing activities. Lack of parts can be avoided through different inventory management techniques like accurate forecasting, and pre ordering for the parts.
- Invest in Upgrades: This way, a routine evaluation of the continuous need to develop and replace equipment can sufficiently mitigate complications arising from aging equipment. The replacement of obsolete equipment with modern instruments increases the dependability of the product and decreases the rate of failure.
Technology in MRO
Automation and Robotics
- Automated Systems: Maintenance activities can be subdivided into several steps, where utilization of automation would help avoid mistakes and execute several routine steps with high precision. Robotic arms and an automated inspection tool give bargaining power an opportunity to minimize on labor costs and enhance the accurateness of the maintenance system.
- Robotic Inspection: Sensors and cameras are attached to robots that can carry out meticulous examinations where the physical conditions are either perilous or difficult to access. This logical control of robotics of inspection enables proper identification of problems and can. Areas such as, through robotics of inspection the ability to detect problems is boosted and the possibility if proper maintenance is guaranteed.
Predictive Analytics
- Data Utilization: Software solutions allow organizations to use equipment data to determine when maintenance is necessary and other intervals for servicing it. Risk assessment and admittance of preventive measures in the business lowers risks since it involves the use of predictive analytics.
- Condition Monitoring: In conditions of assessing the functional state of equipment, non-destructive methods are employed, which are vibration analysis, thermal imaging, and oil analysis with identification of possible failure signals. Such a method makes it easier for organizations to intervene and avoid unanticipated faults and preventions.
CMMS (Computerized Maintenance Management Systems)
A CMMS or a Computerized Maintenance Management System is another type of maintenance management system.
- Features: Some of the main functions of CMMS are associated with the scheduling of the maintenance tasks, management of inventories, and records. Maintenance management software helps to track, schedule, and plan maintenance jobs and increase the efficiency of organizations.
- Benefits: When it comes to MRO practices, the incorporation of a CMMS system helps in the improvement of the various maintenance activities carried out in the organization.
Case Studies or Examples of MRO
Example 1: Aviation Industry
In the context of the field of aviation, MRO practices are quite valuable when it comes to the maintenance and reliability of planes. Airlines have to have very strict routines of maintenance and checks for compliance with the necessary regulations and to avoid equipment malfunctioning. For instance, an airline can employ business analytics to predict the status of its engines and recommend the dates due for an overhaul of its airplane; it minimizes in-flight breakages, thus enhancing safety for travelers.
Example 2: Manufacturing Sector
In a case of a manufacturing organization, issues such as regular equipment failures and slow production came up. Applying the CMMS system and optimizing its activities in the context of the use of predictive maintenance, the company minimized the time losses and increased the service life of the equipment. The data on equipment conditions given by the employed CMMS system allowed the firm to organize maintenance activities ad hoc and relieve the inefficiencies in production.
Future Trends in MRO
Emerging Trends
- Industry 4.0: It is proving to be a significant factor that has affected MRO practices; for instance, the use of IoT devices and connected sensors. Industry 4. 0 technologies keep an eye on assets, gather data and analyze it for better implementation of maintenance methods.
- AI and Machine Learning: AI and Machine learning have also been applied to analyze big data on the equipment to notice faults that require maintenance much earlier. Application of artificial intelligence in this facet enables organisations to find better schedules of maintenance, cutting the expenses and improving their equipment.
Conclusion
MRO or Maintenance, Repair and Overhaul are some of the best practices to be followed in industries to ensure that machines are in proper working conditions. Thus, recognizing and applying efficient MRO strategies can help improve the safety and decrease the expenses of the organization and turn into a successful result. Otherwise, it will continue to improve the MRO work enhancement and become the key to long-term success along with adaptation of newer technologies.